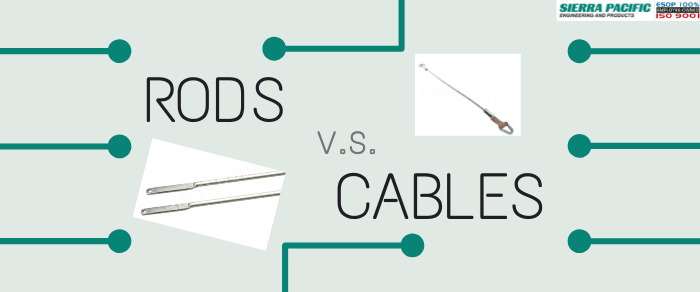
When clients are finalizing design plans for a product that utilizes multi-point latches, they are often unsure what type of connecting hardware would be suitable for their specific application. Your organization may have encountered this conundrum firsthand.
The most common options to link together components in these latching systems are metal cable lanyards or industrial rods. While either solution may be able to get the job done, the linkage option you select can significantly impact product performance. This head-to-head comparison between the two item’s strengths and weaknesses will help you make an informed decision.
The Pros and Cons of Cable Systems
Cable systems have their own unique benefits and drawbacks as compared to other options. Potential uses of cables as a solution are numerous, but they are not perfect for every application. Let’s take a closer look at the detailed attributes of cable systems.
Advantages of Cable Systems
The most noticeable attribute of cables is that they are not rigid the way solid rods are, which comes with some advantages. The rope-like structure of cables takes up much less space than rods and allows them to easily maneuver around (or even through) various other equipment or components on the inside of the door. In addition, this also makes cable systems much easier to transport and handle before being installed. Cables can be tightly coiled to fit neatly in smaller boxes than rods, which can reduce overall freight costs when shipping in bulk. Choosing cables can eliminate some complexity in your supply chain considerations.
Another benefit of cable systems is that they facilitate a very seamless installation. They can be easily hidden by running them low profile against the inside surfaces of the door and also create minimal noise during operation. Cables work great when used with any system which relies on tension to actuate such as rotary latches or spring-loaded slam latches. Lastly, due to their flexible nature cable systems are great at supporting lateral loads. Cables can bend or stretch when pulled in multiple different directions whereas a solid rod might experience extreme lateral stress.
Drawbacks of Cable Systems
Cable systems work well in some cases, but are also not without their shortcomings. Most importantly, cables are typically not as strong as rods of equivalent size and material. The design consisting of many thin metal strings braided together provides ample strength for the lanyard cable itself, but it is susceptible to stretching and fraying. In addition, the weakest point of a cable assembly is typically the crimp where the eyelets are connected, which limits the extent of their durability.
Another important consideration is that while cables are great for pulling, they are unable to push anything the way a rod can. Cables are only compatible with certain types of actuators and latching components and sometimes have more complicated assemblies than rod systems.
Cable systems also have minimum length thresholds. There must be a certain amount of cable between two fittings in order to avoid bunching. ”Bird caging” is the term for a type of distortion where the outer strands of cable unravel and expand to create a birdcage-like shape. Cables are usually custom tailored to a particular application and fewer off-the-shelf options are available for cables than rods. Therefore, cables are not ideal for short-run linkage applications or assemblies that involve certain types of multi-point latches and relatively small doors.
The Benefits and Disadvantages of Industrial Rods
Now, let’s turn our attention to the characteristics of industrial rods. Like cable systems, industrial rods also have their fair share of strengths and weaknesses, which make them suitable for a different selection of applications.
Upsides of Industrial Rods
The most noteworthy advantage of using industrial rods in lieu of cable systems is that they offer superior deflection management. Deflection refers to the degree of displacement that a structural element (in this case, the rod) experiences while under load. Rods are solid and rigid which causes them to allow a significantly lower degree of stretch or bend than cables. This greatly increases their resistance to deformation and makes them perfect for both pushing and pulling components within the assembly.
The rigidity of rods also makes them stronger and more durable overall than cables and not prone to the same types of deformations. Since they are made from a continuous piece of solid material, it is typically easier to modify an off-the-shelf rod to fit your application if needed. Many types of rods can be cut down to length as needed and then painted or touched up to repair any damage to their coating.
Another benefit of the rigidity of rods is their ability to be bent or formed in order to follow a particular path of movement and avoid obstacles inside the door. Rods can also be bent at the ends to apply compression at the latching points. There are a variety of different end-pieces to rods such as roller wheels, studs, or nothing at all which minimizes the number of components in the system and simplifies assembly.
Downsides of Using Industrial Rods
Rods may be simple and effective, but they are not without their disadvantages as well. Industrial rods are inefficient at supporting their weight when installed in long segments. Due to their high weight, lengthy pieces of rod create a large bending moment which can cause them to flex and deform. Intentional bends for the purpose of gasket compression or otherwise may also decrease the overall strength of the rod.
Connecting rods are also more challenging to handle and transport, as they must be packaged in straight, solid segments that are much heavier and larger in size than equivalent cables. This complicates every step of the supply chain including import/export, shipping, warehousing, and assembly of rods.
Compared to cables, rod systems are also very bulky inside the door and can be considered an eyesore in certain applications. Besides that, rods are also susceptible to rattling which can make them very noisy during operation or in applications where vibration is a concern.
Which Hardware Is Right for Your Application?
No part is perfect for every application, and both industrial rods and cable systems have their own distinct strengths and weaknesses. While lanyard cables excel in applications that rely on tension and where flexibility is key, industrial rods offer a strong and rigid solution ideal for a variety of different multi-point latch assemblies.
If you would like some help determining which product offers the best solution for your application, connect with us at Sierra Pacific Engineering & Products, the hardware experts.
Our design engineers can make suggestions to match you with the ideal industrial rod option from our extensive catalog or work with you to design and develop the perfect cable solution as a new custom part. Our comprehensive offering of products and design services ensures that you can find the right solution for your desired application. Contact us today to learn more!
Editor’s Picks
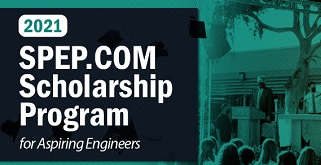
Sierra Pacific Engineering College Scholarship Program
Feb 7, 2022
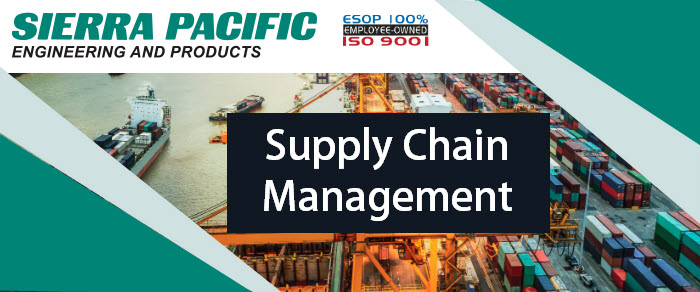
What is Supply Chain Management, and Why Is It Important?
Jan 13, 2022
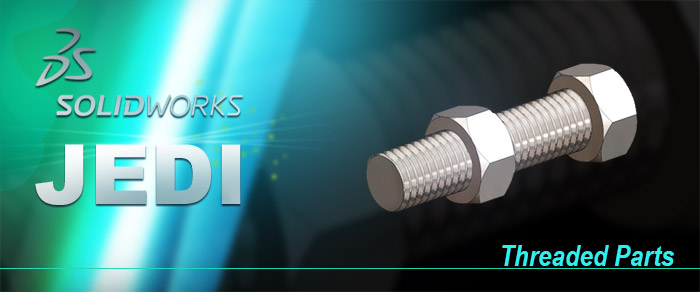
How To Make Threads in Solidworks: Become a Solidworks Expert
Nov 10, 2020