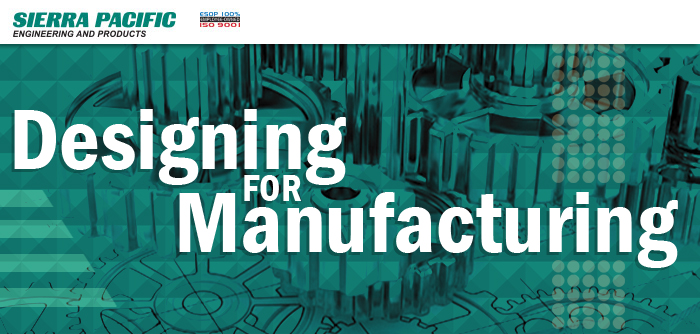
During the product planning and conceptualization process, designers and other stakeholders must bridge the gap between what’s possible and what’s practical.
Just because a particular component can be fabricated doesn’t mean it can be manufactured at scale in a cost-effective and efficient way. That’s why designing for manufacturing (DFM) is so critical to the parts ideation process.
Production design, or design for manufacturing, ensures that production costs are sustainable, the right raw materials are used, and the final product will perform as intended in the specified environments. Let’s further examine what DFM is, along with its core principles and the benefits your organization can unlock by designing for manufacturing.
What Is DFM?
DFM is the process of designing components or parts to maximize ease of manufacturing. The ultimate goal of designing for manufacturing is to yield a higher-quality product at a reduced cost while still maintaining functionality and performance. DFM achieves this by simplifying, refining, and optimizing the product design.
Questioning whether a design is suitable for manufacturing at scale should take place early in your design process. While you can also apply DFM principles later, doing so will be more costly, as you’ll have to alter existing manufacturing processes and potentially engage in significant amounts of retooling. Choosing to apply DFM later could also delay your production process timeline considerably.
Prioritizing DFM early on may require a bit more time upfront, but allows you to avoid headaches and manage costs associated with iterating designs later in the process. When properly applied, DFM principles will also yield a superior-quality product and expedite the overall manufacturing workflow.
For optimal results, designing for manufacturing must include a variety of stakeholders and project participants, including:
- Engineers
- Designers
- Quality Control
- Contract manufacturers
- Raw material suppliers
- Mold/tool builders
- End Users
By involving entities from every level of the design and manufacturing process, DFM allows you to examine the project from multiple perspectives. Each stakeholder can identify potential hidden costs or complications and provide solutions for reducing or eliminating those obstacles.
Designing for Manufacturing: Five Key Components
The DFM framework critically examines five core phases of the design and manufacturing process, including:
1. Process
As the name suggests, this aspect of DFM involves examining the manufacturing process or processes that will be used to create the part. While certain methods may maximize efficiency, they may simultaneously drive up other costs. The goal here is to strike the ideal balance between upfront cost and long term efficiency.
When examining the cost of prospective manufacturing processes, decision-makers should account for two types of expenses: cost per unit and lead time/tooling costs.
For time-sensitive projects, it may be necessary to absorb a slightly higher cost per unit in order to reduce lead time and decrease the amount of retooling needed to enter the production phase.
Choosing the right combination of processes can make or break a manufacturing project. As such, it’s perhaps the most crucial aspect of the DFM framework.
2. Design
As the complexity of the design increases, so, too, does the risk. More complicated designs have more potential failure points and are at a greater risk of needing rework. Such designs also tend to be more costly to manufacture and assemble.
Simplifying the design won’t just reduce costs — it can also promote ease of manufacturing, use, and maintenance. That said, engineers must be careful not to oversimplify the design to the point that it negatively impacts performance or functionality.
When examining the design of a particular component, the multi-disciplinary team must look at everything from consistency and texture to tolerances and material thickness.
3. Materials
After you’ve settled on a process and simplified the design, it’s time to shift your attention to the materials. When selecting your material and finish, you’ll need to consider the following elements:
- Mechanical properties: Mechanical properties include tensile strength, hardness, density, fatigue resistance, and ductility. Choosing the appropriate levels of each property is vital for ensuring final design quality and appropriate budget.
- Aesthetics: The aesthetic appearance of the material will largely come down to the finish. Examples of common finishes include zinc plating, black powder coat, or electropolishing.
- Color: The material’s color must be carefully chosen to ensure that it matches the rest of the product. Another important consideration is the optical properties of the component, such as whether it’s matte and textured or glossy and reflective.
- Thermal properties: What level of heat or burn resistance does the material need to exhibit? Answering this question will help you choose the right raw materials for your design to perform adequately in the eventual application.
- Conductivity: Does the material need to act as a conductor or insulator? This consideration is important for both compliance and performance purposes.
Choosing the ideal material and finish combination will have a profound impact on product lifespan, durability, and useability. With that in mind, you’ll want to carefully research each material option and how it will impact the product application before making your final decision. If necessary, connect with an experienced third-party design team to get assistance.
4. Environment
Will your product be used in frigid sub-zero environments or hot, humid climates? To ensure proper performance and function, your component must be designed to withstand the conditions to which it will be exposed. If your product will be used in a variety of operating conditions, make sure you account for each potential use case.
Imagine that you’re designing access hardware for a recreational vehicle, for example.
In all likelihood, your customer base will use your RV in a wide range of climates and environments. To optimize customer satisfaction, you must ensure that your equipment will maintain its integrity and continue to function correctly regardless of what it’s subjected to. How the product will be used in real life is the most important design input!
5. Testing
The testing/compliance phase is where the rubber meets the road for your DFM strategy. Before you can move onto this phase, you must obtain samples of a prototype part.
Once you receive your prototype order, put it through its paces, exposing it to various real-world conditions to see how it holds up. Additionally, you must verify that the prototype complies with relevant quality and safety standards. For instance, if you’re making electrical enclosures, you’ll need to confirm that your products aren’t overly conductive and are sealed against moisture and dust.
Thoroughly testing and verifying compliance ensures adequate performance and can help you avoid incurring any civil liability as the result of negligent manufacturing processes.
Benefits of Designing for Manufacturing
Designing for manufacturing can help you meet many operational goals, including the following:
Reduce Costs
Is your chosen combination of materials and design processes the most cost-effective way to build a viable product? If not, the DFM model will help you identify and eliminate sources of waste to reduce your manufacturing costs.
Keeping costs in check will help you increase profitability and pass savings on to your customer. While the per-component savings may seem small, applying DFM principles to an entire project can save you hundreds and enable you to offer your product at a more competitive price point.
Facilitate Mass Production
Designing for manufacturing not only reduces unnecessary costs but also expedites the production process. During the early stages of DFM, stakeholders will review the initial design choices to confirm that it’s ready for mass production.
If the chosen manufacturing process requires a significant amount of lead time or substantial retooling, stakeholders will explore alternatives to speed up production. Including raw materials vendors in the design process will also ensure that you can efficiently source supplies to support production.
Ensure Parts Reliability and Functionality
The DFM framework can help you identify unnecessary complexities within your design or manufacturing process.
You and your multi-disciplinary team can pinpoint material shortcomings, inefficiencies, and flaws that may impact product performance. By identifying and removing these issues, you can optimize parts reliability, functionality, and compliance.
Additionally, designing for manufacturing involves extensive testing. Engaging in testing allows you to verify that your design functions as intended and can hold up when exposed to environmental factors such as moisture or extreme temperature. Ultimately, DFM yields a better product and provides a better experience for end users.
Expedite Product Development
Designing for manufacturing is a systematic methodology intended to expedite end-to-end product development. By addressing all facets of a design, including material selection, environmental factors, and compliance, you can avoid the need for major design overhauls and get your component into production sooner.
Expediting the product development workflow through the DFM framework can help you keep your project within budget and on pace to meet key deadlines. In the long run, the biggest source of project delays is the need to repeat previous steps multiple times due to milestone rejections or testing failures.
That said, don’t hesitate to go back to the drawing board if your prototype falls short of compliance, performance, or durability standards. Designing for manufacturing is an iterative process that should be applied cyclically to optimize product performance and functionality.
SPEP: Designing for Manufacturing, Delivering for Clients
At Sierra Pacific Engineering and Products, our talented in-house team of engineers and supply chain experts has mastered the art of designing for manufacturing. From the initial design phases to final production, we leverage core DFM principles to streamline our manufacturing operations and deliver exceptional products to our industrial clients.
Over the years, SPEP has created an extensive catalog of reliable, precision-engineered components and access hardware. Additionally, our talented engineering team can assist with prototyping and design support for proprietary custom designs. Whether you need a reliable, ready-to-manufacture solution or a custom piece of hardware, the SPEP family of employee owners can deliver.
Want to learn more? Contact our team today and let us know how we can meet your access hardware needs.
Editor’s Picks
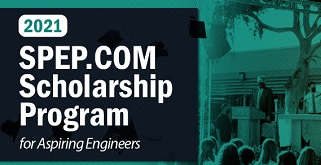
Sierra Pacific Engineering College Scholarship Program
Feb 7, 2022
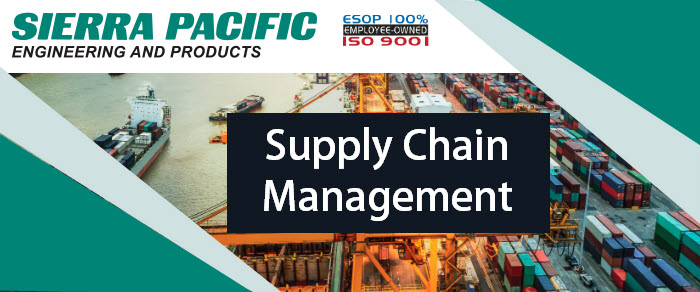
What is Supply Chain Management, and Why Is It Important?
Jan 13, 2022
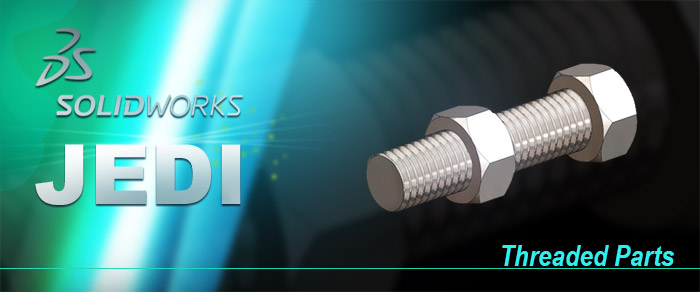
How To Make Threads in Solidworks: Become a Solidworks Expert
Nov 10, 2020