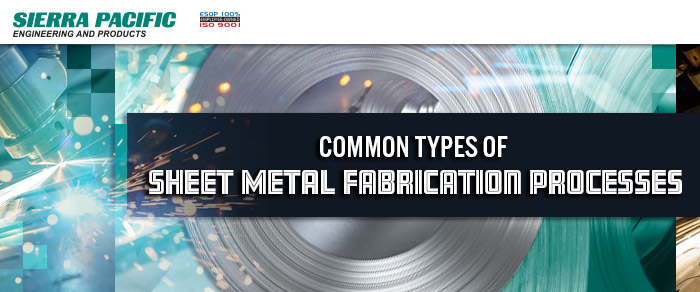
There are many ways of working with sheet metal to transform it into useful components. Each sheet metal fabrication process offers unique advantages in manipulating the material differently for particular applications. However, not everyone is familiar with all of the different fabrication strategies available.
We have outlined some of the most common sheet metal fabrication processes to help our business partners and prospects better understand how coils and sheets of raw materials are transformed into a multitude of different quality industrial hardware items used in their assemblies.
Project leaders and decision-makers must have a general understanding of these various processes to more effectively oversee important projects. Working with SPEP on finding the right part for your application or collaborating with our engineers on new custom designs becomes even easier once you know the basics.
Most Common Sheet Metal Fabrication Processes
Stamping
Stamping is the most common fabrication process associated with sheet metal. During the process, a press will push a tool or die through the subject material in order to create the desired shape, much like a cookie cutter. Manufacturing of almost all sheet metal hardware parts includes stamping in some capacity, which is often used in conjunction with other fabrication processes in order to create the final product.
Punching
Punching is a sheet metal fabrication process that is used to create holes or other perforations in the source material. A powerful press will “punch” out holes so that the product can be fastened to other components. This is essentially the same process as stamping, except with punching the final product is the remaining material where the hole was created and not the piece that was removed during the process.
Forming
Forming is a general term that refers to distorting metal in order to create a certain shape. Sheet metal can be formed by bending, rolling, drawing, stretching, and more. During forming, the source material will take on a new shape without any material being added or removed. Most sheet metal parts are created using a combination of different types of stamping and forming processes.
Bending
Bending is a type of forming which adds basic angles or curves to a workpiece to transform linear pieces of material into dynamic shapes. Depending on the intended application, metal is often bent into ‘U’ or ‘V’ shapes. Bending is used to create a broad range of commercial products and hardware. Because the designs produced by bending are very simple, it is typically a very cost-effective fabrication method with minimal tooling required.
Deep Drawing
Deep drawing is another specific forming process very similar to stamping, except the tool or die does not push all the way through the workpiece. The die will typically have a tapered end which is designed to stretch the metal and thin it out without rupturing the surface of the sheet. Drawing is typically performed without using a heat source in a process known as “cold drawing.” The result is components with a deep pocket or cavity which resemble a cup or pan and may have visible signs of stretching in certain areas.
Rolling
Rolling is a variation of forming which passes sheet metal through a series of rollers that incrementally changes the shape of the workpiece through multiple steps. The equipment used for this process is called progressive tooling. Although it is much more expensive to develop than traditional forming dies, it effectively lowers the cost per unit in high-volume manufacturing by improving the speed and efficiency of the process. This is a highly automated process by utilizing large rolls of sheet metal called coils and sometimes even incorporating other processes such as stamping into the same line of tooling.
Welding
Welding is a mechanical joining process that employs pressure and heat to combine two or more sections of metal together. The most commonly used types of welding are tungsten inert gas (TIG) welding, metal inert gas (MIG) welding, and stick welding.
TIG welders are equipped with a fixed tungsten electrode rod that creates an arc to weld the metals together by consuming a separate piece of handheld filler rod. Modern MIG welders require a machine-fed solid wire electrode which acts as the filler material and is consumed during the process. MIG welding creates fewer fumes and is faster than other welding types but is only suitable for use on homogeneous materials.
Stick welding uses a consumable flux-coated electrode “stick” which eliminates the need for bottled shielding gas used in MIG or TIG welding. An electric current is run through the electrode which creates an arc when it contacts metal.
Shearing
Shearing is simply another term for cutting, ripping, or tearing material apart from itself. This process can be done using a blade, a tool, or another machine. Shearing will often cause burrs or slag on the edges of the material which should be removed by secondary processes such as tumbling or deburring before the product is distributed to the client.
Laser Cutting
Laser cutting is a highly advanced method of cutting or shearing sheet metal using highly amplified laser light. This process is extremely precise, making it an appealing option when working with small or intricate parts. It is also very efficient and causes minimal damage to the subject material.
Plasma Cutting
Plasma cutting is a process somewhat similar to laser cutting but uses high-heat plasma to cut the workpiece. This is also very effective and typically lower cost than laser cutting but causes a build-up of slag on the cut edges of the source material, which must be removed upon completion.
Waterjet Cutting
As the name suggests, waterjet cutting uses an ultra high-pressure jet of water to cut the subject material. Waterjet cutting can be used to fabricate parts out of a broad range of materials into any shape. It can also cut through thick sheets of material, making it a great option for large-scale commercial applications. Waterjet cutting is a very environmentally friendly process that produces no heat or harmful debris.
Cost-Effective Industrial Access Hardware from SPEP
At Sierra Pacific Engineering and Products, we use these sheet metal fabrication processes to manufacture top-quality industrial access hardware for our clients. We have a massive catalog of products, including latches, hinges, handles, locks, and more.
In addition, our engineering team is highly experienced with these and other specialized production processes and can use these strategies to create custom hardware for your company’s intended application.
If you would like to learn more about all the different ways we make parts from sheet metal and other types of materials or need more information on our product lineup, contact SPEP today.
Editor’s Picks
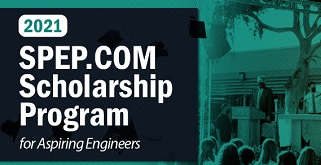
Sierra Pacific Engineering College Scholarship Program
Feb 7, 2022
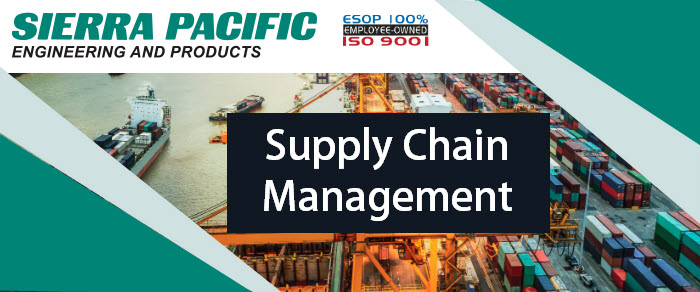
What is Supply Chain Management, and Why Is It Important?
Jan 13, 2022
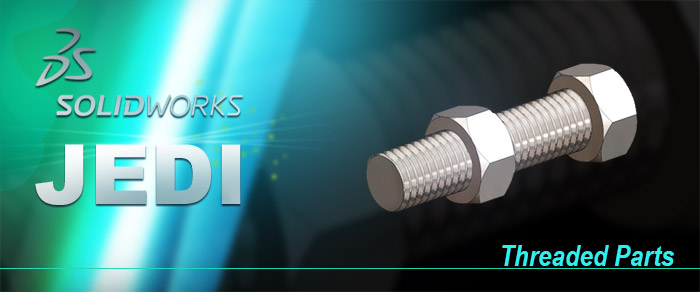
How To Make Threads in Solidworks: Become a Solidworks Expert
Nov 10, 2020